THE HOW YARN IS MADE
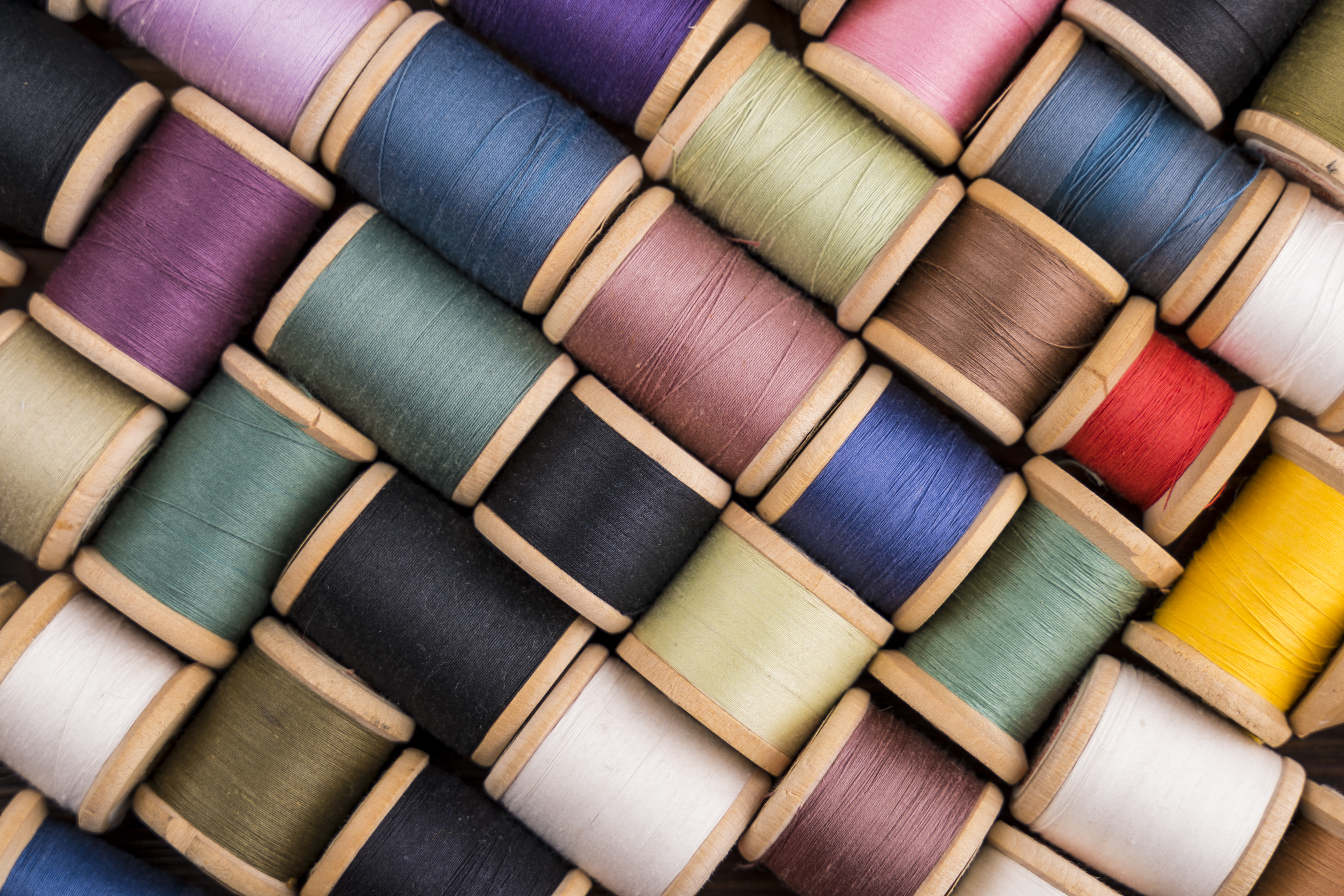
Yarn is a type of fiber. It is made from several twisted threads. The process of spinning involves converting fibres into yarn. This is done with a spinning wheel or machine which takes the raw material (usually in the form of roving or sliver) and twists it together to make a continuous strand. The strength and consistency of the yarn will depend on the twist created during this process as well as how evenly its spun. This step can also determine whether you end up with a single-ply or multiple yarn.
Throughout the spinning process, machines and spinners can control different aspects of their yarn. They can vary the fibre type and weight to determine the final product, as well as set the twist direction and level. Additionally, they can choose to add additional fibres to their thread while it’s being spun. All these choices come together to create unique yarns with endless potential for creative projects.
Yarn can also be spun by hand in addition to using machines. This is done with a spinning wheel or drop spindle to twist the fibres together and create thread. Spinning your own yarn is both satisfying and economical, as it allows you to customize colors, textures, and weights. No matter how it spun all yarn will go through the same steps before being ready for sale: cleaning and preparing the fibers carding or combing them into strips spinning them on a machine or by hand dyeing winding them onto cones or balls smoothing and packing them up for shipping. By understanding this process and its variations you'll have the foundation you need to make informed decisions while shopping for yarn.
WHAT IS YARN MANUFACTURING
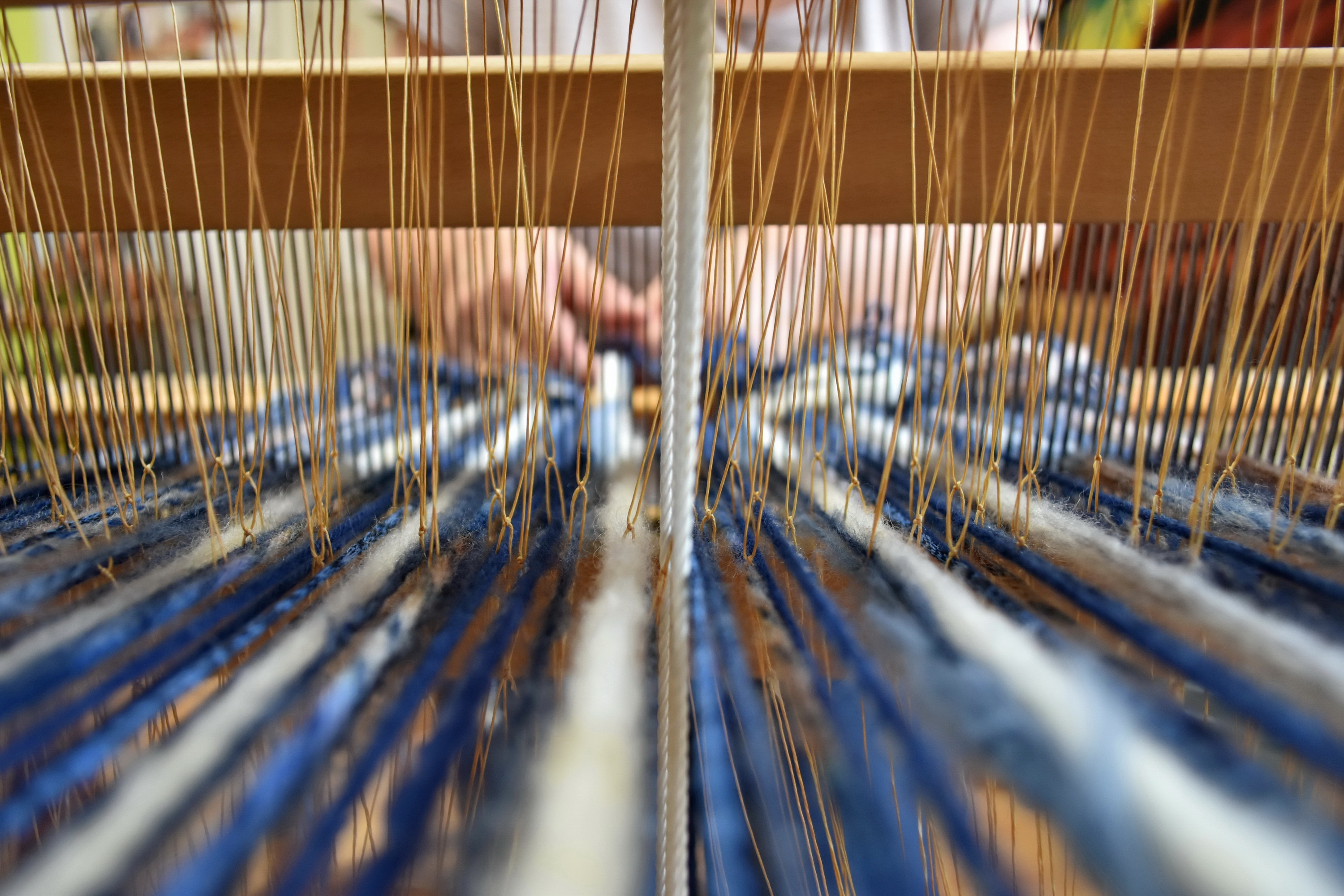
Yarn manufacturing is the process of turning raw fibres into yarn. For clean, strong, and uniform yarns, several methods are required in modern textile markets. This can be done in various ways, depending on the type of fibre and desired quality of the yarn. Different processes are used for man-made or synthetic, animal or plant fibers, as well as blends or mixes of different materials. By understanding the different processes involved in yarn production, you will be able to make more informed decisions when choosing yarns for your projects.
To ensure the highest quality yarns, professional manufacturing of yarn will perform tests to measure the durability and strength, as well as any special properties that may be applicable. Fibers are also tested for colorfastness and chemical content to meet regulations within a particular country or industry. Even after production is complete, the manufacturing of yarn can still be subject to additional processing in order to achieve specific weights, lengths, or textures. It is through these fine-tuning processes that we can create the most versatile and pleasant yarns possible.
OVERVIEW OF YARN MANUFACTURING
Leaping Frog consulting is a reputed service provider in India Yarn manufacturing is a complex process for creating yarns of various types and textures. Manufacturing of yarn, the processes vary depending on the type of fibre being used. For animal fibers, wool and silk require scouring, carding, and combing processes before they can be used in spinning. Synthetic fibers such as acrylic and polyester typically go through a melt spinning process that pre-spins fibres directly from the yarn producer. After either of these processes, fibre is ready to be spun into usable yarns for knitting and weaving.
The spinning process creates yarns of various sizes, textures, and properties, as determined by their end use. For example, yarns intended for beginner knitters such as babies typically use a soft two-ply merino wool, whereas more advanced projects use four- or eight-ply yarns that are stronger and more durable. Another typical spinning method is the cable ply, which uses multiple single threads to create an extra strong overall plied yarn. Once spun, many specialty treatments can be applied to the yarn, such as waxing, dyeing, tweeding, and softening with lanolin, to increase performance levels based on its intended usage.
THE HOW YARN IS MADE?
The process of spinning involves converting fibres into yarn. This is done with a spinning wheel or machine, which takes the raw material (usually in the form of roving or sliver) and twists it together to make a continuous strand. The strength and consistency of the manufacturing of yarn will depend on the twist created during this process, as well as how evenly its spun. This step can also determine whether you end up with a single-ply or multiply yarn.
Throughout the spinning process, machines and spinners can control different aspects of their yarn. They can vary the fibre type and weight to determine the final product, as well as set the twist direction and level. Additionally, they can choose to add additional fibres to their thread while it’s being spun. All these choices come together to create unique yarns with endless potential for creative projects.
In addition to machines, people can spin yarn by hand. This is done with a spinning wheel or drop spindle to twist the fibres together and create thread. Spinning your own yarn is both satisfying and economical, as it allows you to customize colors, textures, and weights. No matter how it’s spun, all yarn will go through the same steps before being ready for sale: cleaning and preparing the fibers; carding or combing them into strips spinning them on a machine or by hand dyeing winding them onto cones or balls; smoothing and packing them up for shipping. By understanding this process and its variations you'll have the foundation you need to make informed decisions while shopping for yarn.
SPINNING PROCESSES AND TECHNIQUES
Spinning is the process of manufacturing yarn from extracted fibers. The manufacturing of yarn involves spinning. In general, it involves taking fibres of varying length and twisting them together to form a continuous strand of yarn. This process is performed on specialised machines called spinning frames. Along with spinning, many additional processes may be incorporated for further quality assurance, such as dyeing, tightening, and finishing. Additional techniques are also used to create special properties within the fibre for enhanced durability, breathability, or insulation.
Once the fibre has been scoured and pre-processed, the spinning begins. There are a few different spinning techniques used in manufacturing of yarn. Ring spinning is one of the oldest methods used in spinning, where in fibre are wound onto large spindles to produce yarns with an even thickness. Ball-winding is another technique used to make small batches of yarn without using a spinning wheel or spindle. This process involves winding roving or top into finished balls of yarn. Finally, rotor-spinning is a mechanical process that is faster than traditional ring spinning and can create thicker, loftier fibre for use in knitting or weaving.
Each spinning process uses different techniques to produce a variety of yarns for use in weaving, knitting, sewing, and other craft projects. Ring spinning produces wrinkle-free yarn with an even thickness throughout the entire length of the yarn. This method employs multiple spindles and is ideal for creating heavier weight yarns with consistent texture. Ball winding is a great option for small batch production, as it doesn't require any machinery or a spinning wheel. For bulkier fiber projects, rotor spinning is a great option for creating fibers that are thicker and loftier than those produced by ring or ball winding processes.
There is also the woollen yarn manufacturing process, which produces a lightweight and soft yarn that comes with the ability to trap air between fibers, creating insulating layers. It's ideal for knitting projects requiring warmth and some give, such as sweaters or scarves. Traditional worsted yarn is produced on an open-end spinning machine and provides superior stitch definition due to its tighter twists. Worsted weight yarns are more durable than woollen spun yarns and can be used for a variety of projects. Finally, hand spinning gives you complete control over the outcome of your project, allowing you to create unique customized yarns with no additional machinery required. Ultimately, the type of spinning process you choose depends on the desired outcome of your project.
THERE ARE MANY DIFFERENT TYPES OF YARN MANUFACTURING.
- Spinning yarn: The first step in the manufacturing of yarn is yarn spinning. Raw materials, such as cotton, wool, and silk, are spun into yarn using a spinning wheel. The yarn is then twisted into a variety of shapes and sizes.
- Knitting yarn: Yarn knitting is the process of making yarn from individual fibers. Fibers are pulled from a skein of yarn and then knitted together.
- Weaving Yarn: Yarn weaving is the process of creating a yarn from a series of parallel threads. To make a fabric, the threads are woven together
- Dyeing Yarn: The process of dying yarn involves colouring it. Dyes are applied to the yarn while it is still in the skein. This process is often used to create unique colors for yarns
- Crochet Yarn: Crochet yarn is made from multiple threads of yarn that are twisted together. This type of yarn is usually used for crochet projects such as afghans and scarves.
CONCLUSION
In conclusion, yarn manufacturing is a complex process that involves various stages, including spinning, twisting, winding, and dyeing. Understanding the different types of yarns and fibers used, as well as the production techniques, can help you make informed decisions when choosing yarns for your next knitting or weaving project. From natural fibers like wool and cotton to synthetic options such as polyester and nylon, the possibilities are endless.